What is Digital Twin Technology in Manufacturing?
In today’s ever-changing world of smart manufacturing, businesses must adopt cutting-edge technologies to remain competitive. One of the most transformative technologies in recent years is Digital Twin Technology. But what exactly is Digital Twin Technology in manufacturing, and how can it reshape the way products are designed, manufactured, and maintained?
At its core, a Digital Twin is a virtual replica of a physical product, system, or process. This digital copy mirrors real-world operations and continuously collects and updates data from the physical world. It enables manufacturers to simulate, predict, and optimize their operations, leading to improved decision-making, reduced downtime, and more efficient production processes. In other words, Digital Twin Technology in manufacturing bridges the gap between the physical and digital worlds, allowing for real-time insights and data-driven innovation.
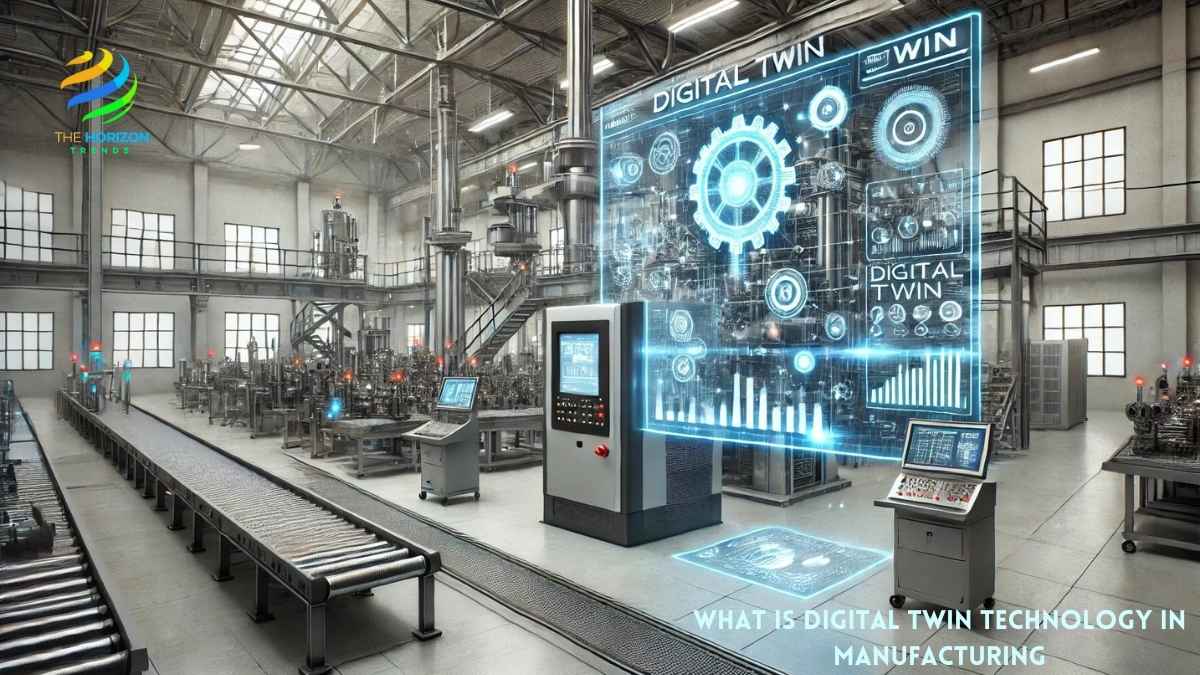
In the realm of smart manufacturing, Digital Twin Technology is revolutionizing how companies operate. According to Siemens, a pioneer in automation and digitalization, a digital twin serves as a virtual representation of a physical product, system, or process, enabling manufacturers to optimize performance and innovate efficiently. Learn more about Siemens’ Digital Twin Overview.
In this article, we’ll take a closer look at how Digital Twin Technology works, the benefits of Digital Twin in manufacturing, and examples of how it’s being used today. Let’s dive deeper.
What is Digital Twin Technology in Manufacturing? – An Overview
To understand what is Digital Twin Technology in manufacturing, picture a factory where products are moving through various machines, each with its own set of variables. A Digital Twin captures data from these machines—temperature, speed, pressure, material quality, and more—and creates a virtual model of the factory floor. This digital model updates in real-time, reflecting every change and adjustment that occurs in the real world.
Manufacturers can then use this digital twin to:
- Simulate different scenarios: They can test how changes to equipment, raw materials, or operational procedures will impact the production line.
- Predict potential failures: By analyzing historical data and real-time performance, the system can forecast when equipment might break down and suggest maintenance before the issue escalates.
- Optimize processes: Continuous monitoring allows for constant fine-tuning of production, reducing inefficiencies and boosting output.
Simply put, Digital Twin Technology in manufacturing is all about using data to mirror, simulate, and improve the production process.
Digital Twin in Manufacturing Example
A practical Digital Twin in manufacturing example can be found in the automotive industry. Imagine a car manufacturer launching a new vehicle model. Traditionally, engineers would need to build physical prototypes to test different designs, materials, and production methods. This process is time-consuming and costly.
With Digital Twin Technology, they create a digital replica of the vehicle and virtually test how each component performs under various conditions, such as temperature, pressure, or road impact. They can run simulations to identify weak spots, optimize the design, and ensure the car meets safety and performance standards—all without building a physical prototype.
This is a real game-changer for manufacturers, as it reduces the time-to-market, lowers development costs, and improves the quality of the final product. In fact, automotive giants like BMW and Tesla are already leveraging Digital Twin Technology to streamline their production processes.
But the benefits of Digital Twin Technology are not limited to car manufacturers. This powerful tool is being used across industries, from aerospace to pharmaceuticals, to improve efficiency and reduce costs.
Benefits of Digital Twin in Manufacturing
The benefits of Digital Twin in manufacturing are numerous, especially as more manufacturers adopt Industry 4.0 technologies. Here are some key advantages:
1. Improved Product Development
By using Digital Twins, manufacturers can test and iterate on designs without the need for multiple physical prototypes. This allows for faster innovation and reduced product development cycles.
For example, a Digital Twin can simulate how a product will perform under stress, heat, or other environmental conditions. This means engineers can spot design flaws early on and make adjustments before the product is ever physically produced.
2. Enhanced Efficiency
With a Digital Twin, manufacturers can continuously monitor and analyze production processes. This real-time feedback helps optimize equipment settings, reduce waste, and minimize energy consumption.
In essence, a Digital Twin allows for constant fine-tuning of production, leading to higher efficiency and lower operational costs.
3. Predictive Maintenance
Rather than waiting for equipment to break down, a Digital Twin can predict when a machine might fail. By analyzing performance data, the system can forecast potential issues and suggest maintenance before problems arise, reducing downtime and saving on costly repairs.
4. Better Decision-Making
Because Digital Twins provide real-time data, manufacturers can simulate various scenarios to assess the impact of changes. This data-driven approach enables smarter decision-making and reduces the risk of costly mistakes.
5. Increased Customization
In today’s market, customers increasingly demand personalized products. Digital Twin Technology allows manufacturers to customize products without sacrificing quality. By simulating how different designs will perform, manufacturers can offer tailored solutions that meet customer needs.
The overall benefits of Digital Twin in manufacturing are clear: greater efficiency, cost savings, and improved product quality.
Digital Twin Technology Companies
Several Digital Twin technology companies are leading the charge in bringing Digital Twin Technology to the manufacturing industry. Here are a few notable names:
1. Siemens
Siemens is a leader in Digital Twin technology through its Siemens Digital Industries Software. Their platforms enable manufacturers to design, simulate, and optimize their production processes.
2. General Electric (GE)
GE uses its Predix platform to monitor industrial machines, analyze data, and predict equipment failures. This helps manufacturers maintain peak performance and reduce downtime.
3. PTC
PTC’s ThingWorx platform integrates Internet of Things (IoT) capabilities with Digital Twin Technology to provide real-time insights into equipment and production performance.
4. Ansys
Ansys Twin Builder allows companies to simulate everything from individual products to entire production systems, making it easier for manufacturers to optimize efficiency and reduce operational costs.
5. Dassault Systèmes
With their 3DEXPERIENCE platform, Dassault Systèmes offers robust tools for building and managing Digital Twins across industries, enabling companies to optimize product performance and streamline their operations.
These Digital Twin technology companies are helping manufacturers around the world adopt Digital Twin Technology and unlock the full potential of smart manufacturing.
Digital Twin Software
Choosing the right Digital Twin software is essential for building accurate, real-time simulations of manufacturing processes. Here are some key features manufacturers should look for when selecting Digital Twin software:
- IoT Integration: The software should integrate seamlessly with IoT devices on the factory floor to collect and process real-time data.
- Data Analytics and Visualization: A good Digital Twin software should offer robust data analytics and easy-to-understand visualizations. This makes it easier for teams to gain insights from the data and make informed decisions.
- Simulation Capabilities: The ability to simulate various scenarios and test different outcomes is a must-have feature in Digital Twin software.
- Scalability: The software should be scalable to grow alongside your business, allowing for future expansion and integration with new technologies.
- Security: With Digital Twins collecting sensitive data, robust security measures are essential to protect against cyber threats.
Popular Digital Twin software platforms include Siemens Simcenter, Ansys Twin Builder, and ThingWorx, each offering unique features to help manufacturers optimize their processes.
Digital Twin vs Simulation
One common question is: What’s the difference between Digital Twin and simulation? While both are used to model and predict performance, there are critical differences between the two.
- Simulation: A simulation is a static model that tests specific scenarios under controlled conditions. It can be run repeatedly but doesn’t update with real-time data.
- Digital Twin: A Digital Twin is a dynamic, real-time model that continuously updates with data from the physical world. It reflects current conditions and can adjust predictions based on ongoing performance.
In essence, while a simulation provides a snapshot of potential outcomes, a Digital Twin offers a live, constantly evolving model of how something is performing. This real-time data makes Digital Twin Technology far more powerful and practical for manufacturers seeking to optimize operations and make informed decisions.
As explored in my previous blogs on emerging technologies like nanotechnology and smart manufacturing, the integration of Digital Twin Technology further exemplifies how advanced tools are reshaping industries, enhancing efficiency, and driving innovation. By leveraging these technologies, manufacturers can unlock unprecedented insights and capabilities, paving the way for a smarter, more connected future.
Why You Should Invest in Digital Twin Technology in Manufacturing
If you’re in the manufacturing industry, there has never been a better time to invest in Digital Twin Technology. The ability to create a virtual replica of your products, equipment, or processes—and use real-time data to optimize them—offers endless possibilities.
Digital Twin Technology can help you:
- Improve product quality
- Reduce downtime with predictive maintenance
- Optimize processes for greater efficiency
- Enhance decision-making with real-time data
- Customize products to meet customer demands
Leading Digital Twin technology companies offer a wide range of Digital Twin software that can help you integrate this technology into your business. From predictive maintenance to process optimization, the benefits of Digital Twin in manufacturing make it an essential tool for the future.
Investing in Digital Twin Technology in manufacturing is an investment in innovation, efficiency, and business growth. Don’t wait—start exploring the benefits of Digital Twin for your company today.
Frequently Asked Questions (FAQs):
What are the technologies used in digital twins?
Several advanced technologies come together to create Digital Twin Technology. Some of the most critical include:
Internet of Things (IoT): IoT devices, such as sensors, collect real-time data from physical objects or environments. This data is sent to the Digital Twin, allowing it to accurately reflect and simulate the real-world system.
Artificial Intelligence (AI) and Machine Learning (ML): AI and ML are crucial for processing large sets of data and making predictions based on patterns. They allow Digital Twins to learn from historical and real-time data, improving decision-making and optimization.
Big Data Analytics: Digital Twins process vast amounts of data generated by IoT devices, production systems, and other sources. Big data analytics helps to extract actionable insights from this data.
Simulation Software: Software platforms such as Ansys Twin Builder, Siemens Simcenter, and ThingWorx are used to create virtual simulations that model the behavior of physical objects or systems in real-time.
Cloud Computing: Cloud-based platforms offer the scalability needed to process large amounts of data and run complex simulations. Cloud computing also enables easy access to the Digital Twin from different locations.
Augmented Reality (AR) and Virtual Reality (VR): AR and VR technologies help visualize Digital Twins in 3D, allowing manufacturers to interact with the virtual replicas of their systems in a more intuitive way.
These technologies together make Digital Twins not only possible but also highly effective for real-time monitoring, simulation, and optimization.
How are digital twins used in manufacturing?
Digital Twins play a crucial role in modern manufacturing by offering a virtual replica of physical assets, processes, or entire production lines. Here are a few ways in which Digital Twin Technology is used in manufacturing:
Product Development: Manufacturers use Digital Twins to simulate the performance of products before they are physically built. This allows engineers to test various designs, materials, and configurations, identifying potential issues early in the development process.
Predictive Maintenance: By continuously collecting data from machines on the factory floor, a Digital Twin can predict when equipment is likely to fail or require maintenance. This reduces unplanned downtime and helps extend the lifespan of machinery.
Process Optimization: Digital Twins enable manufacturers to analyze and optimize their production processes in real-time. By simulating different scenarios, manufacturers can identify inefficiencies and adjust parameters to maximize output and minimize waste.
Supply Chain Management: Digital Twins can be used to create a digital representation of the entire supply chain. This provides real-time visibility into every step of the process, from sourcing raw materials to shipping finished products, making it easier to predict bottlenecks and optimize delivery schedules.
Customization: As the demand for personalized products grows, Digital Twin Technology allows manufacturers to customize products to specific customer preferences while maintaining high-quality standards and efficient production.
What is digital twin for process industries?
In process industries like oil & gas, chemicals, and pharmaceuticals, Digital Twin Technology is used to model and simulate entire production processes. A Digital Twin for process industries represents not just individual equipment or machines but the entire system of interconnected processes.
For example, in a chemical plant, a Digital Twin could mirror the entire production line, from raw material inputs to the final chemical product. This digital replica monitors real-time data such as temperature, pressure, and flow rates, allowing operators to:
Optimize the process flow: By simulating different operating conditions, they can determine the most efficient way to run the plant.
Ensure safety: A Digital Twin can predict potentially dangerous conditions, such as pressure build-up or overheating, and trigger preventive actions to avoid accidents.
Improve product quality: Process industries rely on consistent production standards. Digital Twins help maintain tight control over process variables, ensuring the quality of the final product.
By optimizing production and preventing costly shutdowns, Digital Twins are an invaluable tool for process industries.
What are the 4 types of digital twins?
There are generally four main types of Digital Twins, each serving different purposes within the manufacturing lifecycle:
Component (or Parts) Twins: These are the most basic form of Digital Twins. They represent individual components or parts of a system, providing insights into how a specific piece of machinery or equipment is performing.
Asset Twins: These models combine several Component Twins to form a Digital Twin of an entire asset, such as a machine or a vehicle. Asset Twins track how the components within an asset interact and operate as a whole.
System (or Unit) Twins: A System Twin represents a group of assets working together within a larger system. For example, a System Twin might model an entire production line, showing how different machines interact to produce a product.
Process Twins: Process Twins go beyond individual machines or systems. They model entire production processes, integrating data from various systems and assets. This allows manufacturers to simulate and optimize complex processes, ensuring efficiency from start to finish.
These types of Digital Twins can work independently or in tandem, providing different layers of insights and optimizations at various levels of the manufacturing process.
What is digital twin in semiconductor manufacturing?
In semiconductor manufacturing, Digital Twin Technology is used to improve the production of microchips and other electronic components, which require extreme precision and high-quality control.
A Digital Twin in this industry creates a digital replica of semiconductor manufacturing processes, such as lithography, etching, and wafer handling. Here’s how Digital Twins are applied in semiconductor manufacturing:
Yield Optimization: Semiconductor fabrication is complex, and even small variations can lead to defects in chips. Digital Twins help monitor and control every aspect of production, ensuring that the final product meets tight quality standards while maximizing yield.
Equipment Performance: Semiconductor manufacturing equipment needs to operate with minimal deviation. Digital Twins collect data from this equipment to predict when parts might wear out or require recalibration, reducing downtime and extending equipment lifespan.
Process Control: Digital Twins can simulate different manufacturing scenarios, allowing engineers to test how adjustments to temperature, pressure, or material properties will impact the final product. This is essential for maintaining consistency and reducing defects.
Product Design Validation: Digital Twins allow engineers to design and test new semiconductor devices in a virtual environment before moving to production. This reduces the time and cost associated with developing new microchips.
In the fast-moving world of semiconductor manufacturing, where even the smallest error can lead to costly rework or product failure, Digital Twin Technology is indispensable for maintaining precision and efficiency.